Blog
Modernizing Quality: Insights from the U.S. R&D and Quality Summit 2024
Oct 01, 2024 | Mike Jovanis
Oct 01, 2024 | Mike Jovanis
More than 2,400 life science quality leaders across 440+ companies convened at the Veeva R&D and Quality Summit in Boston to connect, learn, and collaborate with peers and Veeva experts. The Quality zone highlighted elevating quality beyond compliance, with customers and partners offering their perspectives on achieving operational excellence throughout the product lifecycle. Topics included modernizing QC labs, advancing GxP training, improving digital validation management, enhancing external collaboration, leveraging AI and advanced technologies, and more.
Questioning convention: Moderna’s shift from ‘No way’ to ‘Why not?’
During the opening keynote, Moderna spotlighted its quality transformation journey from a small-scale biotech to a global player. Jennifer White, senior vice president of global quality, emphasized how the Moderna mindset — focusing on the right people and partners, questioning convention, and reducing friction — guided their system rebuilding, process modernization, and workflow simplification.
Moderna focused on efficiency and adopting Veeva’s best practices to successfully revamp its system at unprecedented speed while also modernizing its batch release process within Vault. It was an incredible story of shifting from “No way!” to “Why not?” as the company modernized 13 quality processes across 12 business units, touching 5,700+ employees in 16 months – in half the time it originally expected.
“We shifted into a period of incredible rapid growth, and as we grew at an unprecedented rate we had to maintain a high level of quality… We never sacrificed quality for speed because we had that base camp (integrity, quality, and respect). It helped us stay grounded.” Jennifer White, Senior Vice President of Global Quality, Moderna
Watch the Quality zone keynote to learn more about Moderna’s quality transformation journey.
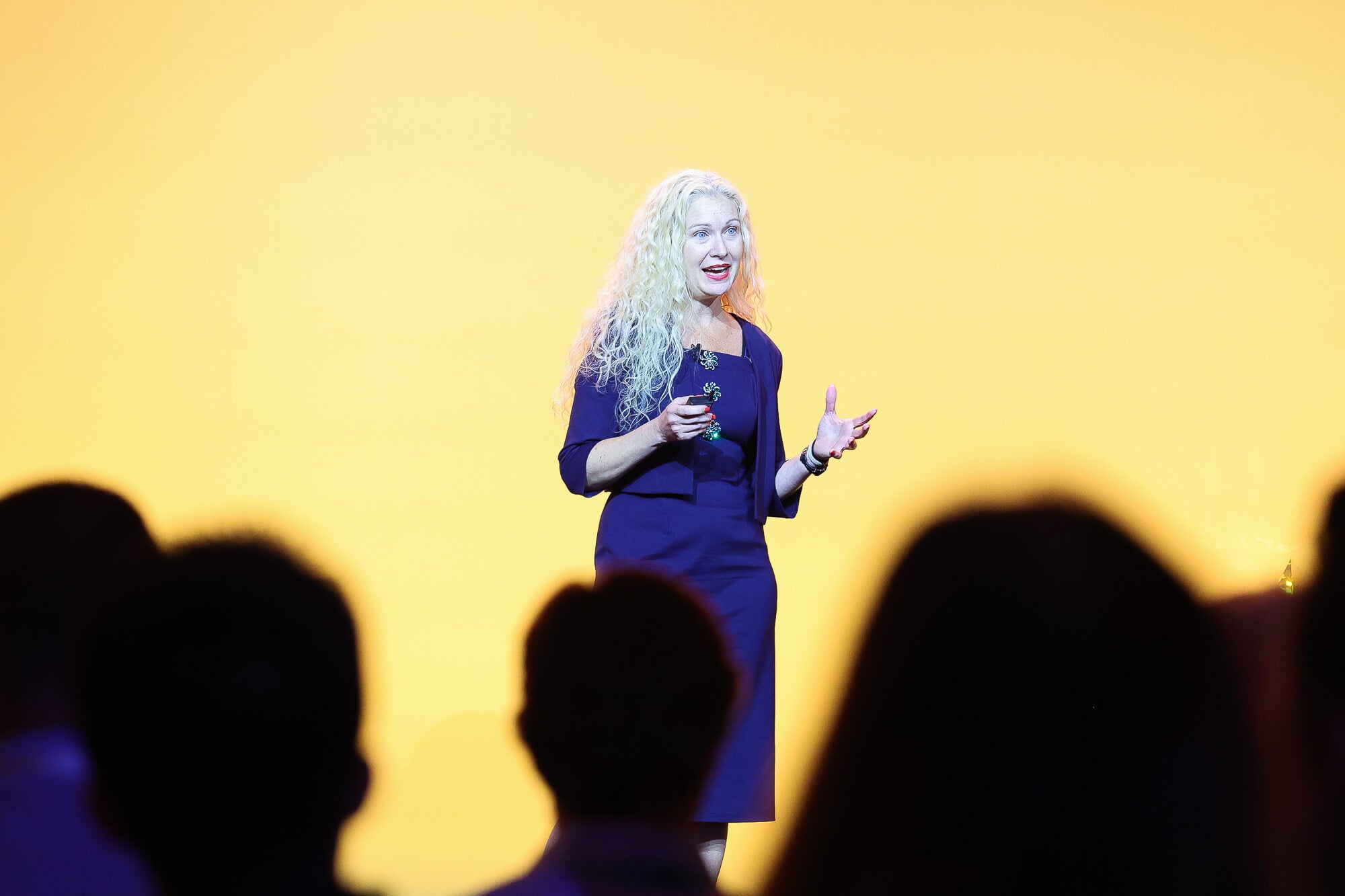
Moderna’s Senior Vice President of Global Quality Jennifer White presenting the Quality zone keynote, September 2024.
I concluded the keynote with an overview of Veeva’s Quality vision and strategy, emphasizing the value of unification. Key advancements were highlighted in new product areas, including Vault LIMS, which is now ready for larger customers, Vault Validation Management, achieving a 50% reduction in validation effort, and Vault Batch Release, now available for early adopters.
Explore our roadmap recordings to discover what’s new within the Vault Quality Platform and what exciting updates are coming soon.
Redefining LIMS: Embracing a Single, Unified Solution
New to the Quality zone this year was a dedicated series of QC-specific content, designed to showcase how Veeva’s solutions seamlessly integrate both QA and QC functions. Jason Boyd, senior director Vault LIMS at Veeva, shared how Veeva is redefining LIMS to go beyond what legacy LIMS applications do. Whereas legacy solutions required layers of appended technology, Vault LIMS brings together the functionality of LIMS, QC ELNs, LES, Stability Study Solutions, and Lab Asset Management into a single modern cloud application.
The sessions highlighted how Veeva not only addresses the needs of each area individually but also enhances overall value through increased collaboration and simplified technology.
- Chris Manoogian, quality control associate director at Verve Therapeutics and other panelists offered insights into modernizing their QC processes by moving from paper-based and legacy systems to cloud-based LIMS. They discussed how their transitions are improving laboratory productivity and efficiency while continuing to achieve compliance and allowing for integration with their existing Vault Quality products.
- Alvotech offered thoughtful insight on how it identified the need to pivot from further investing in its legacy LIMS to Vault LIMS, redefine and simplify its business processes, and how to manage that change internally.
See how Veeva is redefining LIMS in this short video.
Session spotlights: Insights on quality and innovation
The event featured 15 diverse customer sessions with speakers representing over 20 different companies. Highlights of the event included:
- PwC and Veeva delivered valuable insights on the practical application of AI and advanced technology in Quality Management Systems (QMS). Carl Ning, Senior Director, Vault QMS Strategy at Veeva, and Sam Venugopal, Partner, Global Quality Lead at PwC, shared use cases of how PwC and Veeva work together to help organizations turn AI ambitions into actionable strategies that enhance quality management.
- In a GxP training panel including Minaris Regenerative Medicine, ReciBioPharm, and others industry leaders, the discussion centered on Vault Training and how moving from fragmented training systems to a unified solution has simplified processes and enhanced quality ecosystems.
- During their panel on shifting to risk-based validation management, members of Amgen shared the transformative benefits of adopting a risk-based validation process to enhance risk management and data integrity governance.
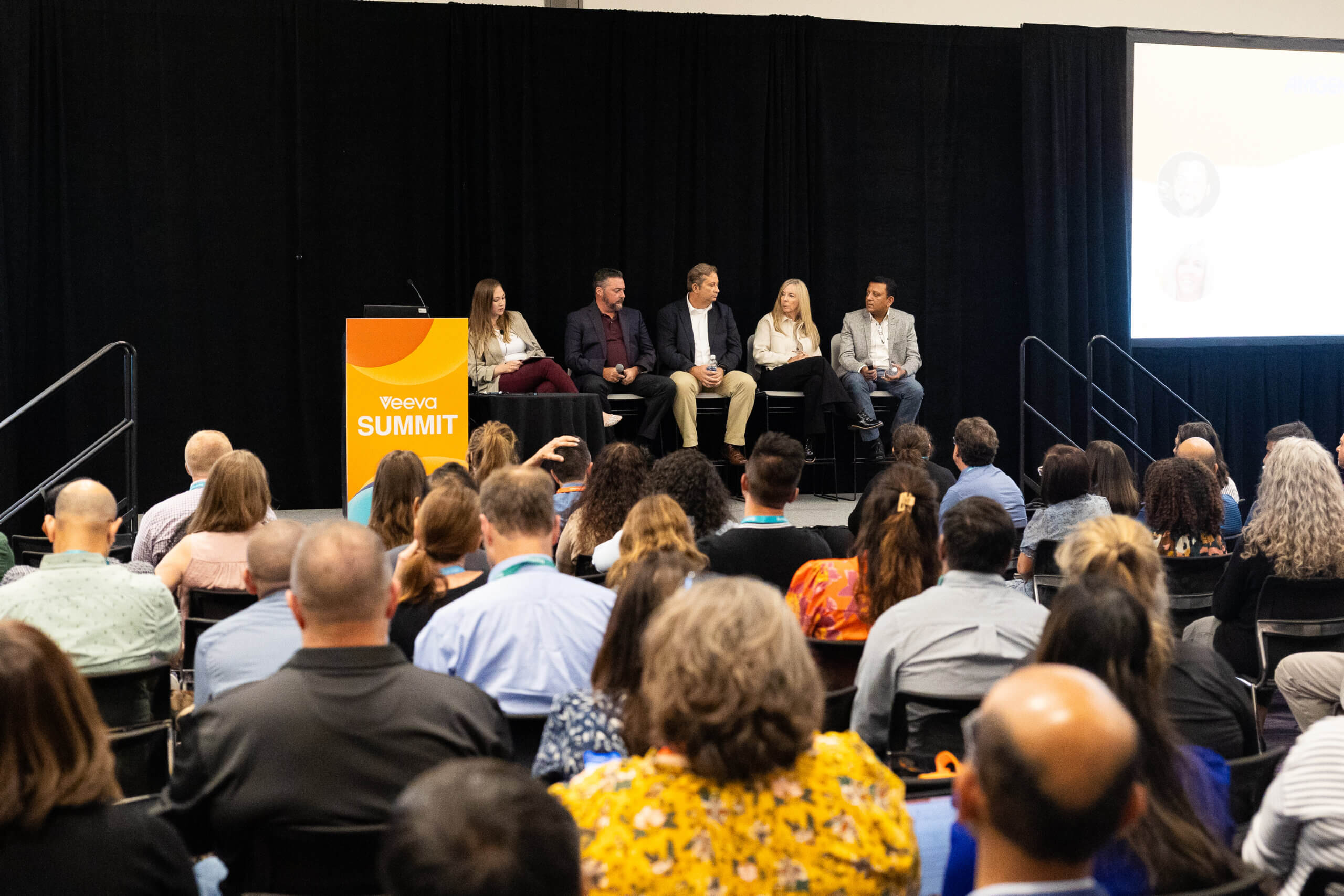
Amgen panelists Jim Gagnon, director of quality systems; Thomas Craig, associate director; Maggie Mahaffy, senior specialist quality; Sudhir Hanwat, senior manager, DTI global quality; and moderator Nina Ricciardelli, director of Vault Validation Management at Veeva, during the panel on shifting to risk-based validation management.
Celebrating Veeva Quality and Manufacturing Heroes
Each year, Veeva honors customers who, along with their teams, have advanced digital transformation in our industry. These Veeva Heroes have pushed the boundaries to improve processes and deliver business impact for their organizations. We celebrated and thanked Veeva Quality Heroes and they shared the following valuable insights with peers:
- Transforming quality systems and processes: Shiraz Laufer, executive director of digital quality at Moderna dove into the details and aggressive timelines of transforming its quality systems and processes with speed while scaling to meet global demand and company growth.
- Implementing with speed and purpose: Ryan Heil, director of quality management at Forge Biologics, rapidly integrated Vault QualityDocs, QMS, Training, Station Manager, and LIMS and is starting to implement Validation Management, positioning the company as a leader in contract manufacturing and operational efficiency. He highlighted how Forge’s adoption of multiple solutions enabled scaling to meet rising customer demands, ensure safe and efficient patient treatments, and enhance client interactions through effective external collaboration.
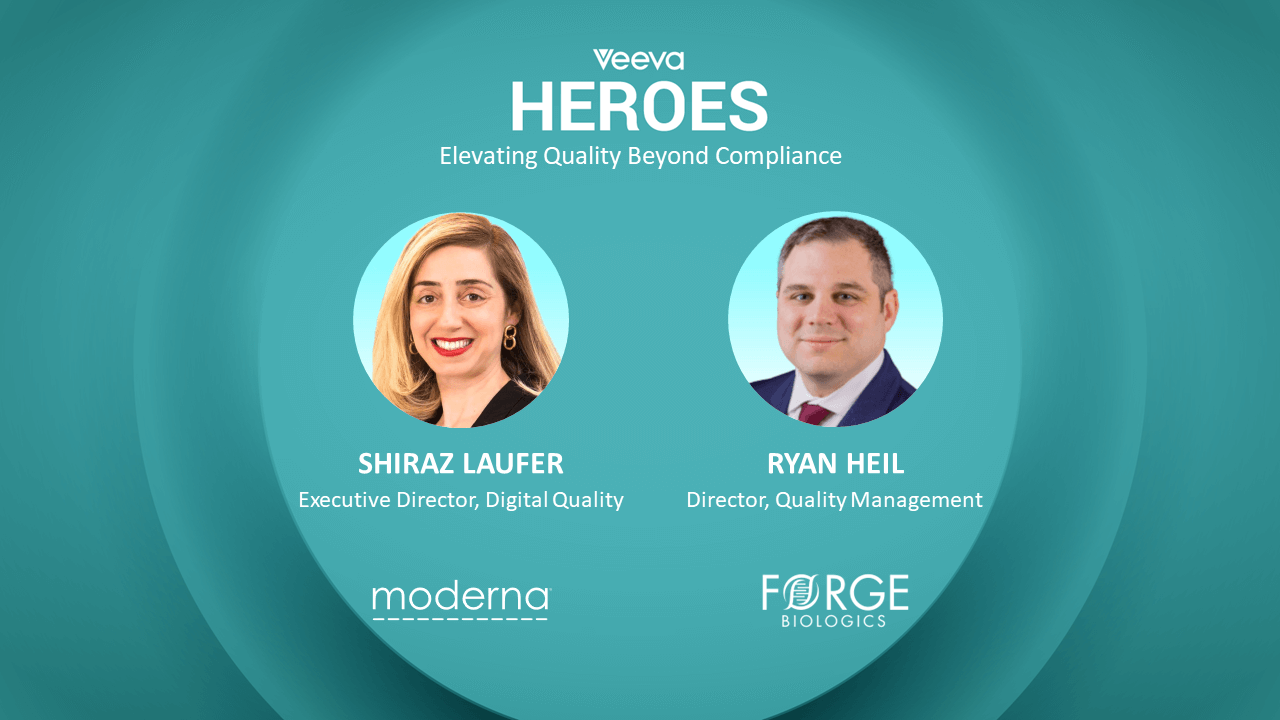
Watch now on Veeva Connect, including Quality zone customer, roadmap, and innovation theater sessions to learn how to elevate quality beyond compliance.